Electroplating Equipment System
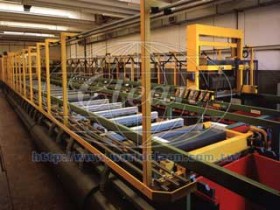
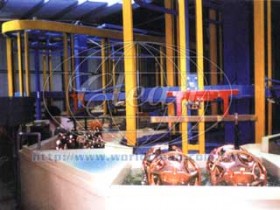
Electroplating is a process of electrolysis which provides the sheet metals of layer metal to function as anode. The electrolyte usually is ion solution plated with metal and the function of workpieces to be electroplated is similar to cathode. After voltage was conducted between anode and cathode, metal ions of electrolyte was attracted to swim to cathode and plated on it after reduction. Moreover, the metal of anode redissolves and provides more metal ion to electrolyte. Under some circumstances the insolubility is used. Flesh electrolyte is added to replenish plated metal ions.
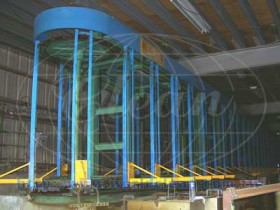
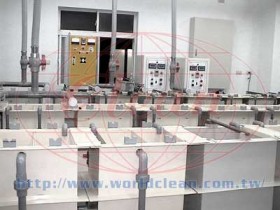
Pre-Surface-Treatment (water-soluble solution)
A general process follows some steps as below ( prepared for degreasing or hot water rinsing) → Main degreasing → water rinsing (1) → water rinsing(2) → surface adjustment → chemical conversion (zinc phosphate) → water rinsing (3) → water rinsing (4) → or adding D.I. water to rinse again. If using ferric phosphate system, surface adjustment is then unnecessary.
Degreasing is surfactant which consists of Alkali and emulsion. Emulsion is to emulsify oil and prevents from poor adhesion, and by means of alkali to set apart from greasy and keep clean. After rinsing the surface part we precede the chemical conversion in order to strengthen the adhesion, erosion resistance.
For the purpose of saving this treatment process, we combine degreasing with chemical conversion into “Two-in-One” (or “Three-in-One”) process. It turns out that non-alkali component of degreasing will remain only emulsion and phosphate. Disposing greasy must rely on the acid component which results from the chemical conversion. Therefore, the solution will be overused, and more important thing is, the quality of treatment can not control any stability. That leads to bad affect on coating.